Cement slurry design parameters Well depth diameter and casing size. Day ÄBSTRÄCT Ä cementbentonite CB slurry cutoff wall is a variation of the slurry wall process that is used to create an underground barrier to stop the lateral flow of ground water and other fluids.
Pdf Cement Bentonite Grout Backfill For Borehole Instruments Semantic Scholar
6 rows bentonite powder.
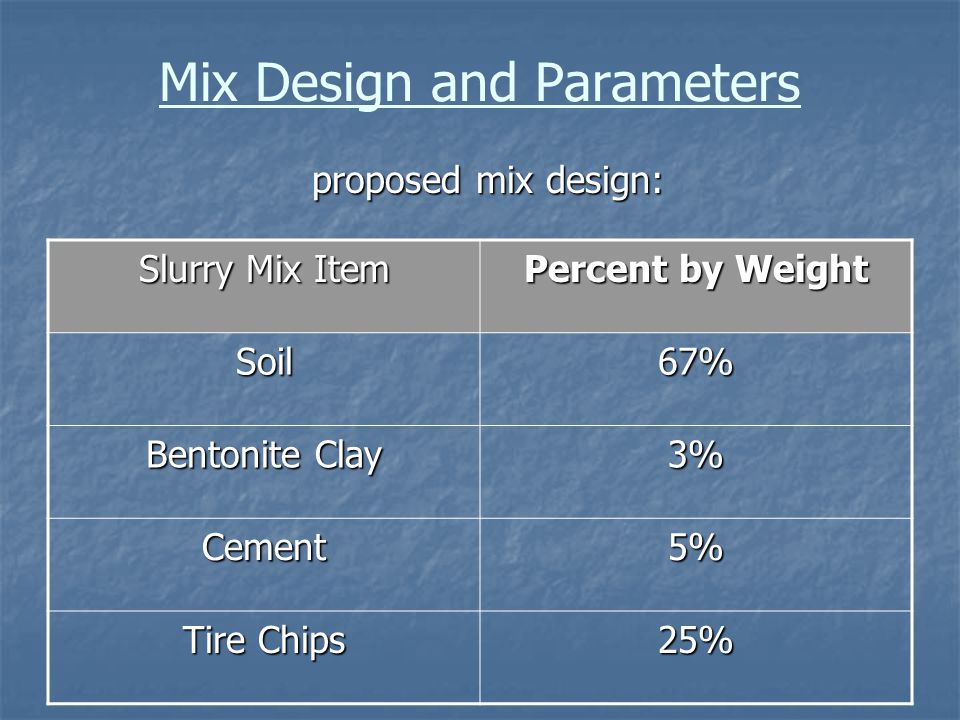
. Lower slurry density from less than 158 down to 115 ppg typically. The mix resulted in 9 percent cementitious materials a watercementitious material ratio WC of 034 and 09 percent bentonite. Bottom hole circulating temperature BHCT.
100 69-72 8-16 Self-hardening slurry Composite wLiner. The optimal cement slurry mix design principle. When mixing on site its imperative to get the water volume with cement powder content right.
If the concentration Cs is expressed as kilograms of bentonite per cubic meter of final slurry then the formula becomes. Water that will be used at the asset. Bentonite cement earthfill sand unpermeable layer.
Most specifications allow for a maximum of 6 gallons of water per 94 pounds one bag of Portland Type 1 cement powder. Permeability test results can be found in the mix design report. The bentonite slurry was mixed in a Hobart mixer.
Bentonite was used in this investigation at 5 10 20 and 25 replacement of cement by weight. At the slurry plant cement or some other setting agent is added to the bentonite slurry. CEMENT-BENTONITE SLURRY WALL MIX DESIGN Christopher R.
The viscosity of the mixed slurry is designed to be in the fluid range during the excavation process. Step 3 adds cement wilkinite soda ash in agitation vat successively in the mass fraction choosing ratio and stirs. The simpler the better.
Slag cement-Bentonite 5 x 10-7. There is a principle that I have always come to appreciate when talking about designing cement slurries. Mix Design Rules In order to keep field procedures simple the emphasis.
Bentonite is typically used at concentrations of 1 to 16 BWOC. Bentonite Slurry in civil engineering. Bentonite slurry shall be prepared by mixing water and bentonite until the bentonite particles are fully hydrated and the resulting slurry appears homogeneous.
5 x 10-7 50 95-120 5-10 Typically remote mix. The bentonite slurry was mixed for a period of three minutes. First here is a handy table to simplify the process of cement slurry design.
The C-B slurry coats the sides of the trench with a thin slippery layer known as a filter cake. BENTONITE ADDITIVE TO CEMENT TABLE Percent Bentonite Gallons of water bags of cement Slurry Yield gallons bag Multiply for bags of Bentonite required Multiply for bags of cement required 10 117 1578 0103 56 8 104 1436 0092 61 6 91 1294 0077 68 4 78 1159 0057 76 2 65 1017 0032 87 0 52 882 0000 100. R an Steven R.
This minimizes the slurry seepage out of the trench and groundwater seepage into the trench. 100 69-72 6-12 Self-hardening slurry Impermix. Commonly the grout mix design is carried out by trialand-error in laboratories-.
The slurry is then pumped from the mix plant to the excavation. The mixture including 10 bentonite 90 sand is the most economical solution that satisfies the limits values needed for clay core of earth fill dams and clay liners of solid waste storage areas. 1 x 10-10 NA NA 7-14 Depth Limitations.
It is one of two extenders that are covered by an API specification. Once the excavation is to full depth the bottom is cleaned and the process moves on. Bottom hole pressure BHP.
Mud density Samples of available cement lot. Storage ponds may be used to hydrate the bentonite slurry. We try to mix it and depending on the depth pump it to the size of tremie pipe used at a ratio of 5⅝ to 5¾ gallons of water.
This principle is easy to remember. Because of the relative simplicity. This combination is frequently utilized to form a solid protective barrier in the ground.
Ps pw 1 C CGp 1 where pw is the specific gravity of the mixing water assumed to be 10 and Gp is the grain specific gravity of the bentonite powder used to prepare the slurry. The final mix design consisted of 180 pounds of cement 51 pounds of flyash 2542 pounds of soil dry weight 50 gallons of bentonite slurry and 312 gallons of reservoir water. Cement shall be added to the bentonite slurry just before introduction in the trench.
Soil-Cement-Bentonite SCB slurry walls have been used with increasing frequency in recent years to provide barriers to the lateral flow of groundwater in situations where the strength of a normal soil-bentonite wall would be inadequate to carry foundation loads. Bentonite is used to. 1 x 10-6 25 70-75 6-12 Self-hardening slurry.
A slurry is a thin sloppy mud or cement or in extended use any fluid mixture of a pulverized solid with water often used as a convenient way of handling solids in bulk. Tolunay-Wong hydrated the bentonite slurry for 4 hours prior to adding it to the soil or to the soil and dry bentonite mixtures. Using bentonite slurry as a permanent filling material ACtrafficengr CivilEnvironmental 1 Jun 11 0836 Usually a cement grout is used for a structural reinforcement or controlled low strength material aka flowable fill if its just filling space.
The addition of cement to the backfill blend allows the backfill to set and form a more rigid system. Water Bentonite clays pozzolans amorphous silica Sodium Silicate etc. Step one adds the water choosing ratio mass fraction in agitation vat.
A preparation method for cement bentonite slurry body preparation comprises the following steps. Bottom hole static temperature BHST. Cement Bentonite Mix Design.
INTRODUCTION If the natural soil does not meet the requirements of the. During construction of the barrier wall a trench is. Bentonite can be added to any API class of cement and is commonly used in conjunction with other extenders.
Soil-Cement-Bentonite SCB slurry walls have been used with increasing frequency in recent years to provide barriers to the lateral flow of groundwater in situations where the strength of a normal soil-bentonite wall would be inadequate to carry foundation loads. In this context this means the use of the less possible additives in their lowest effective concentration that can provide the desired cement slurry. Source water was poured into the mixer and the mixing blade was turned on then bentonite was added.
Step 2 starts agitation vat. If you do not have a gradual hand. Bentonite slurry is a combination of sodium bentonite and slurry.
The C-B slurry is prepared by combining cement with a hydrated bentonite-water mixture just before discharge of the C-B slurry into the trench. Reduction of hydrostatic or greater economy. Cement plus Bentonite Selected for reducing slurry density and increasing slurry volume Normal bentonite additions range from 1 to 12 percent by weight of cement bwoc For every 1 bentonite bwoc added the water content must be increased 065 gallons assumes dry blending Bentonite reduces resistance of cement to.
The addition of cement to the backfill blend allows the backfill to set and form a more rigid system.
Concrete Mix Design Used For Laboratory Tests Download Table
Design Proportions For Sccb Mix Design Program Download Scientific Diagram
Blend Mix Proportions And Blend Slurry Properties Download Table
The Feasibility Constructability And Efficacy Of Tire Derived Aggregate As A Component In Slurry Cutoff Walls Ppt Video Online Download
Pdf Cement Bentonite Grout Backfill For Borehole Instruments Semantic Scholar
All You Need To Know About Bentonite In Cement Slurries Better Well Cementing For All
Sb Slurry Trench Cutoff Wall Schematic Lagrega Et Al 2010 Download Scientific Diagram
Soil Cement Bentonite Slurry Walls Geo Solutions Soil And Groundwater Problems Solved
0 komentar
Posting Komentar